
На одном из старейших предприятий Прикамья — ММК-Лысьвенский металлургический завод — сегодня выпускают необычный металлопрокат. Его главная особенность — расцветка. Причем она может быть не только однотонной, но и имитирующей дерево, камень и кирпич. Электролитически оцинкованный прокат с полимерным покрытием (так официально называется получаемый материал) используют в разных сферах. Из него делают сайдинг для отделки зданий, металлочерепицу и элементы внутреннего оформления вагонов метро.
Как наносят такое покрытие и получают упакованные в рулоны разноцветные металлические ленты шириной до 1600 миллиметров, мы узнали, побывав на заводе.
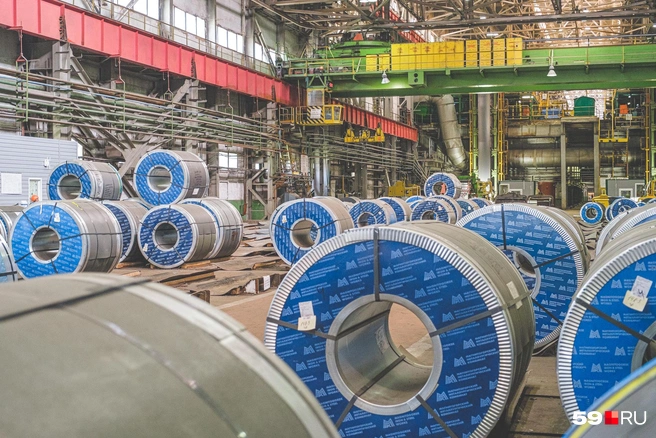

На ММК-ЛМЗ нет отдельных станков, вместо них — огромные агрегаты, объединяющие множество машин. Оцинкованный прокат с полимерным покрытием производят на агрегатах № 3 и 4. Оба — непрерывного действия, то есть работают круглосуточно. Их останавливают, только чтобы провести профилактику. Расстояние от начала до конца каждого агрегата — 1100 метров.
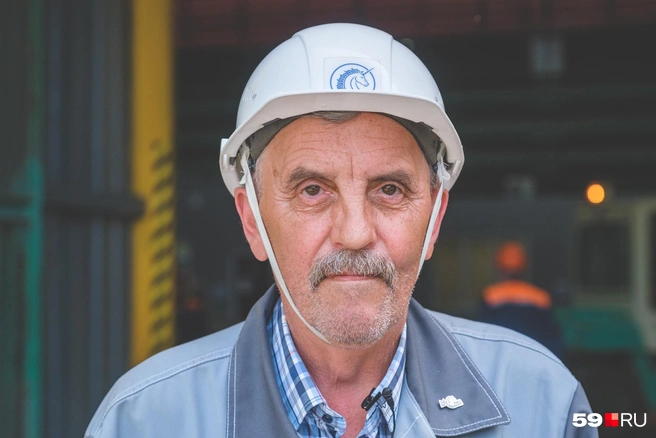
Входные участки обоих агрегатов состоят из разматывателей, сварочной машины и башенного аккумулятора, в котором накапливается металлическая полоса.
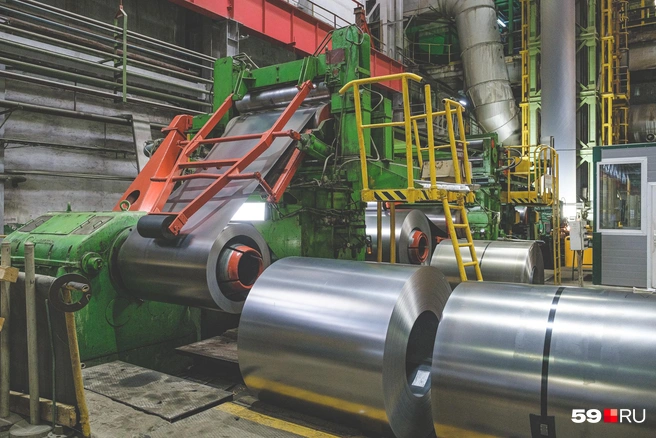
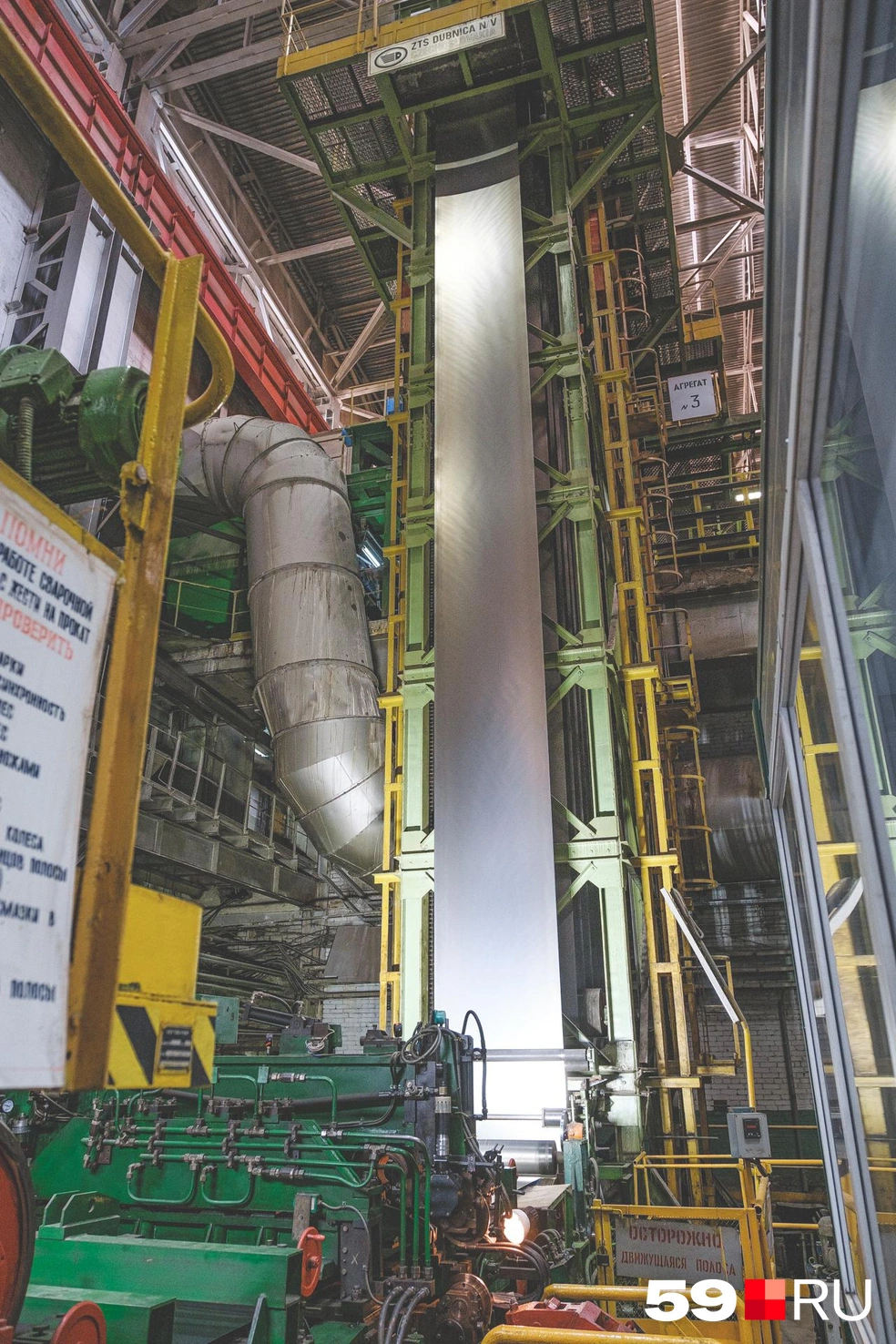
Когда накопитель заполняется, входной участок останавливают, чтобы выбрать всю загруженную металлическую ленту и направить ее дальше. При этом агрегат продолжает работать: пока первый разматыватель стоит, запускают второй. Концы лент из разных рулонов сваривают, чтобы получалось цельное полотно.
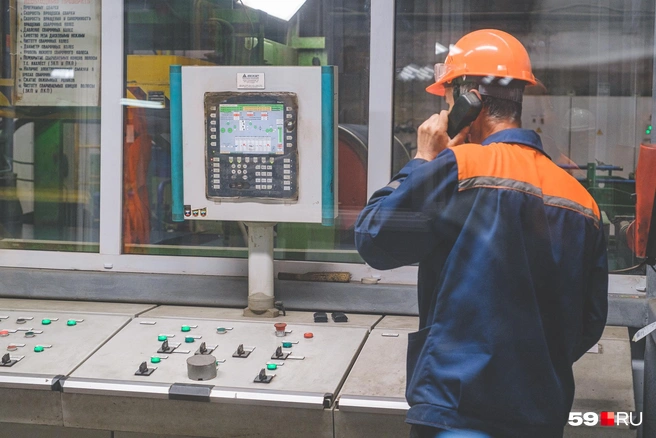
Следующая часть агрегата находится на высоте 9,6 метра. В первую очередь здесь выправляют кромки металлической ленты — так, чтобы не осталось ни намека на волнистость.

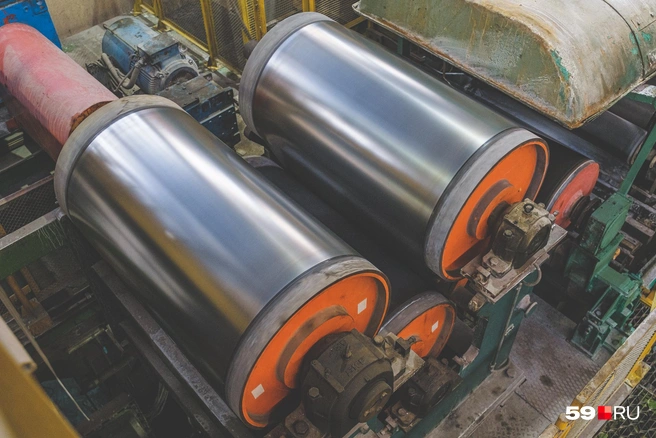
Металл обезжиривают щетко-моечные машины (лента проходит через щелочной раствор при температуре 75 градусов) и протравливают. Очищенная полоса идет на электролитическое цинкование.
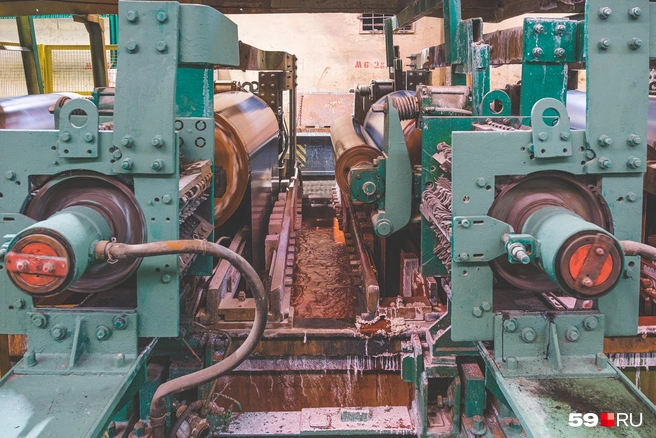
На оцинкованную металлическую полосу наносят защитное хроматное покрытие и отправляют дальше — на окрасочный участок. Там ее грунтуют и отправляют на просушку в печь, которая нагревается до 240 градусов. После охлаждения полоса возвращается, и поверх грунта полиуретановыми роликами наносят лицевую полиэфирную эмаль. Толщину покрытия закладывают в программу. С обратной стороны также наносят эмаль, но другую — эпоксидную.
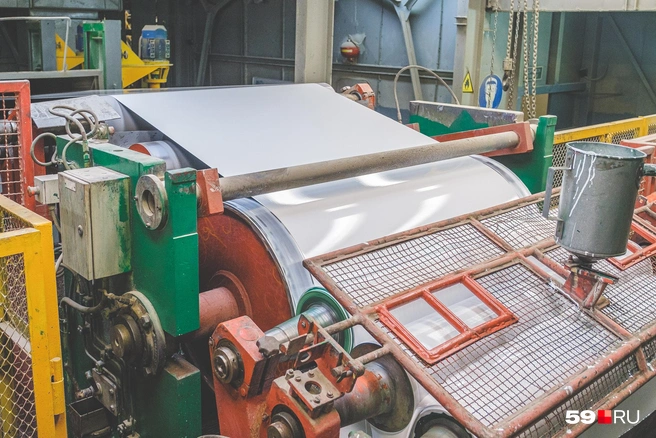
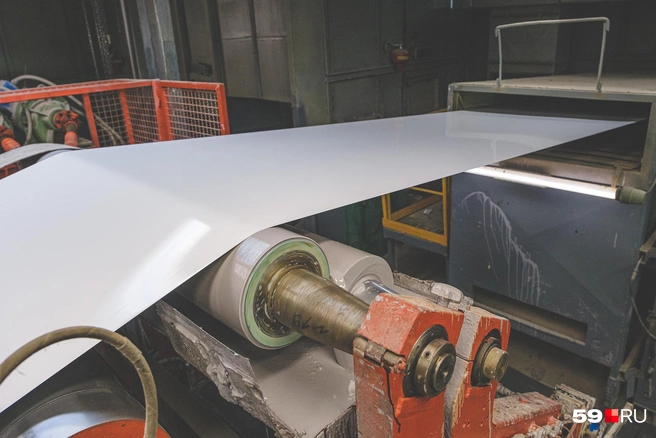
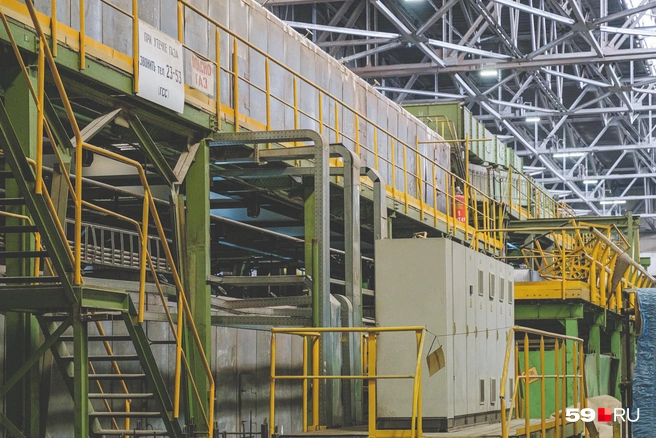
Для полимерного покрытия в основном используют эмали марки «Прайм Топ Индастри», для эпоксидного (которое наносят на внутреннюю сторону) — российские эмали.
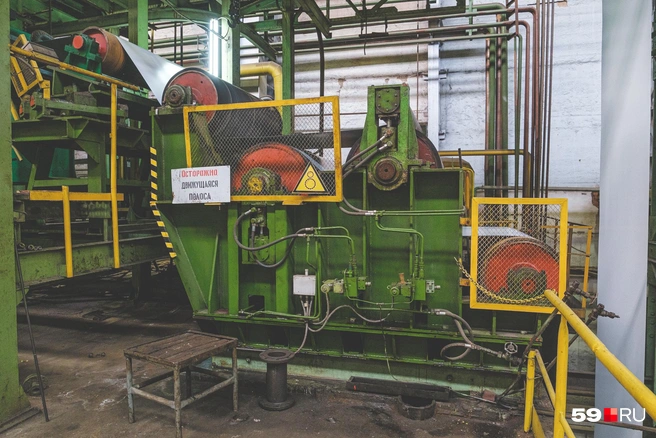
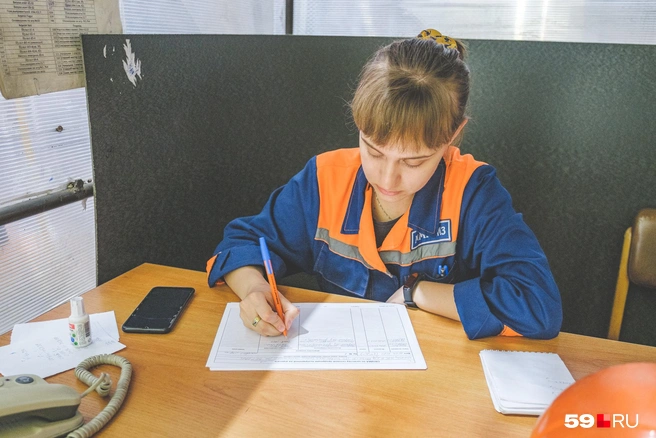
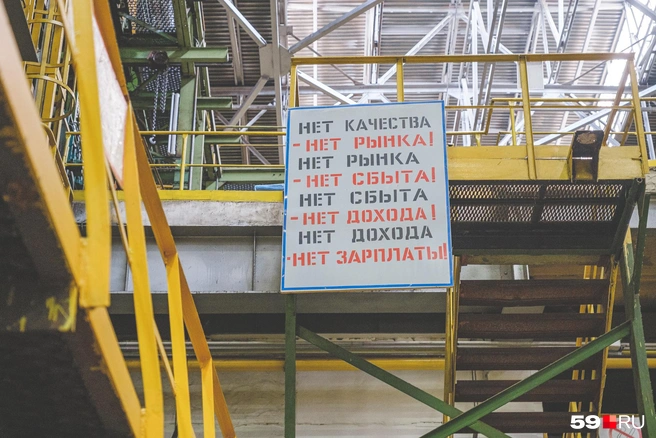
Имитацию кирпичной кладки, поверхностей из дерева и других материалов создают на агрегате декоративных покрытий итальянской компании Danieli. Его запустили пять лет назад, в марте 2016 года. Старт производству SteelArt дал премьер-министр Дмитрий Медведев.
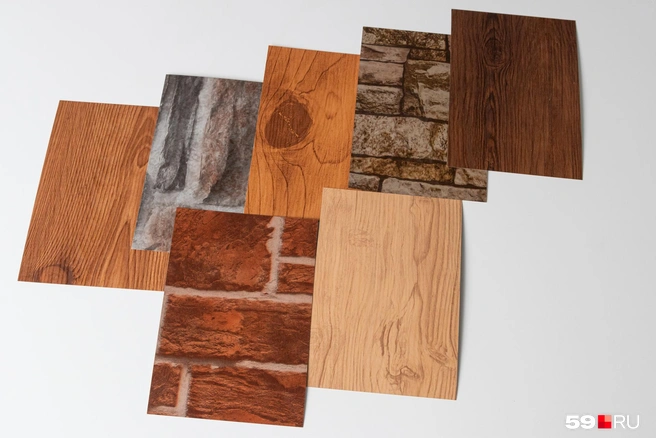
Покрытие наносят на оцинкованный прокат, подготовленный тут же, на ММК-ЛМЗ.
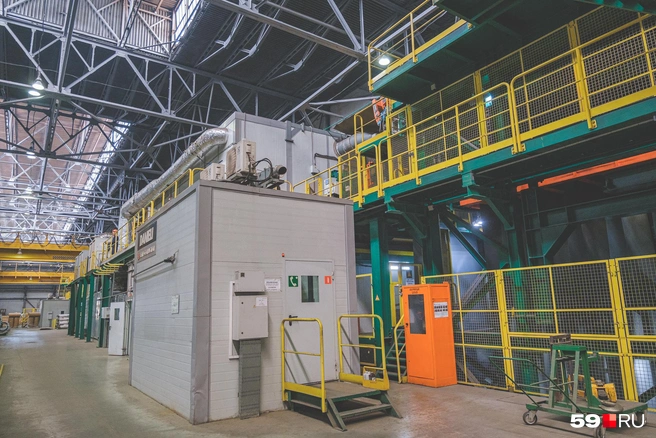
Входной участок производства состоит из двух разматывателей и сшивной машины. Процесс похож на тот, что при производстве металлопроката с обычным полимерным покрытием, но Danieli не сваривает, а сшивает металлическое полотно. Потом лента идет из башенного накопителя на обезжиривание — в щетко-моечную машину. На металл с обеих сторон наносят защитное хроматное покрытие и направляют к машине для нанесения грунта. Далее — в печь и на охлаждение. А затем наносят покрытие.
Четвертый слой после цинкового, защитного и грунтового полимеризуется в печи при температуре 240 градусов, и металлическое полотно идет на участок принтеров. Там на него наносят специальные чернила — так появляется рисунок.
Всего работает три принтера: их сочетание позволяет получать самые разнообразные расцветки. Когда рисунок меняется, новый настраивают по меткам, чтобы краски не смещались и изображение было четким.
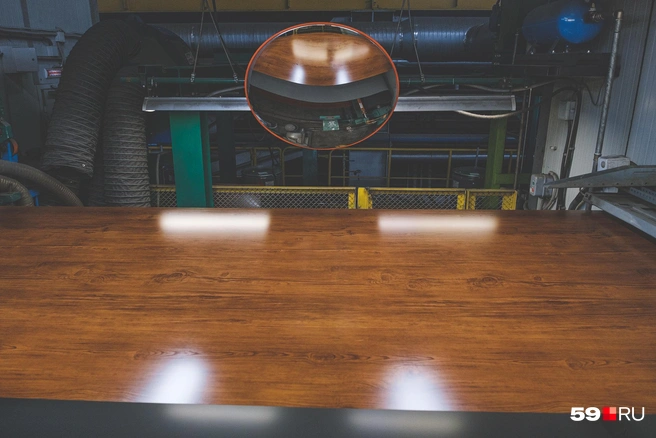
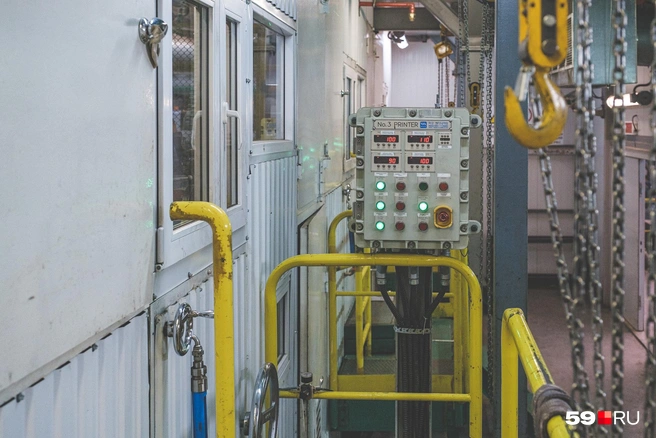
Эффект 3D, когда поверхность не только визуально, но и на ощупь напоминает определенный материал, создается при помощи лакового покрытия. Как только чернила высыхают, полоса поступает на трехвалковую машину, где на нее наносят защитный лак: гладкий, текстурированный или с тем самым 3D-эффектом.
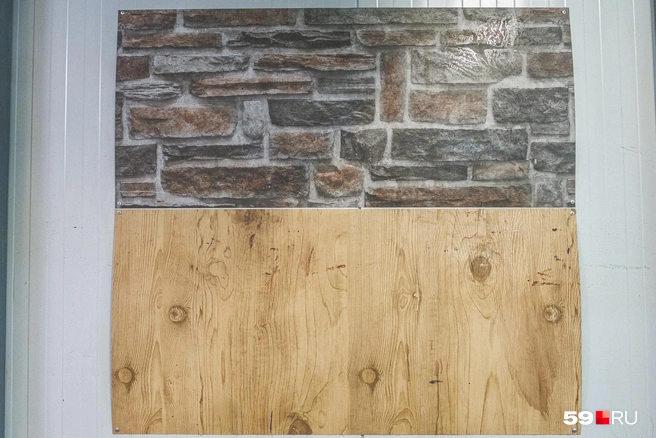
После сушки — финальная лакировка. При необходимости после этого можно нанести рисунок и на обратную сторону: операции пойдут в том же порядке.
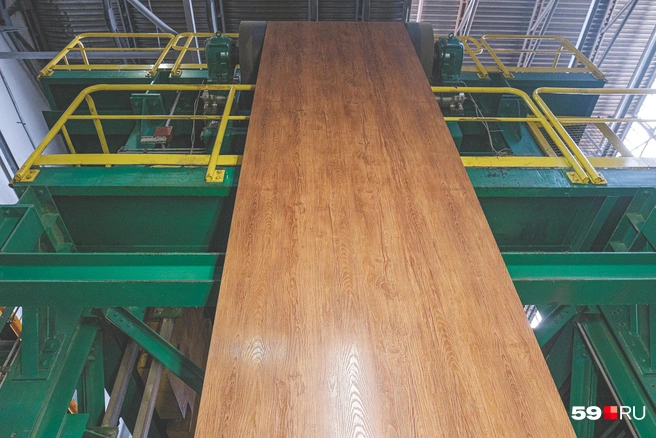
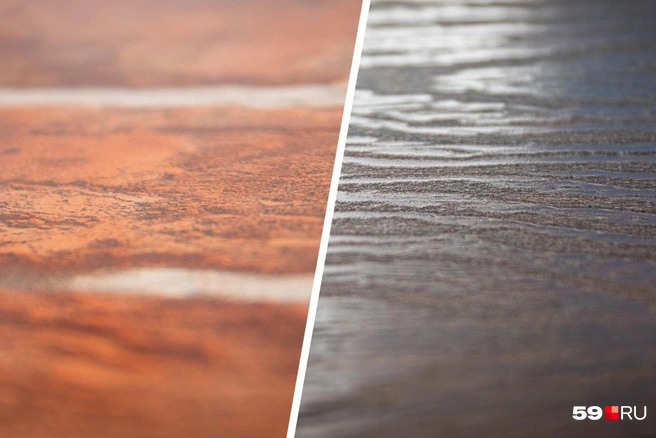
Завершающий этап всех работ — упаковка. Смотанные в рулоны металлические полосы краном приносят на соответствующий участок, где их готовят к отправке клиентам.
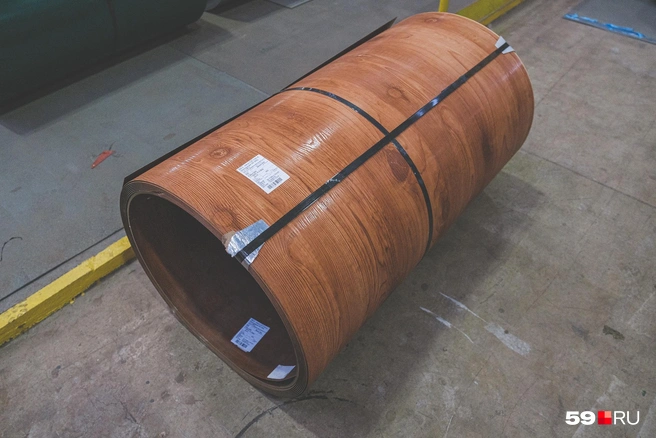
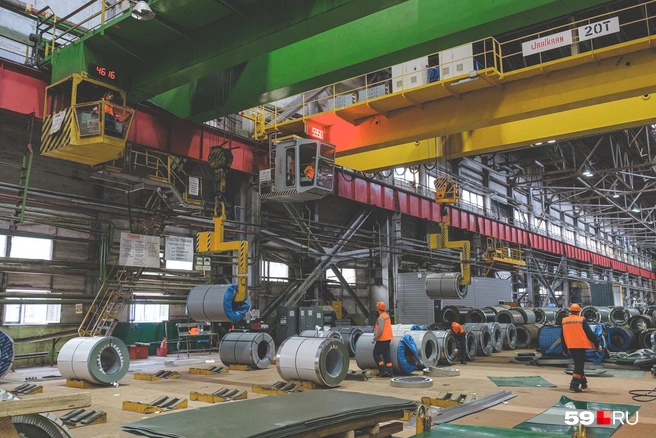
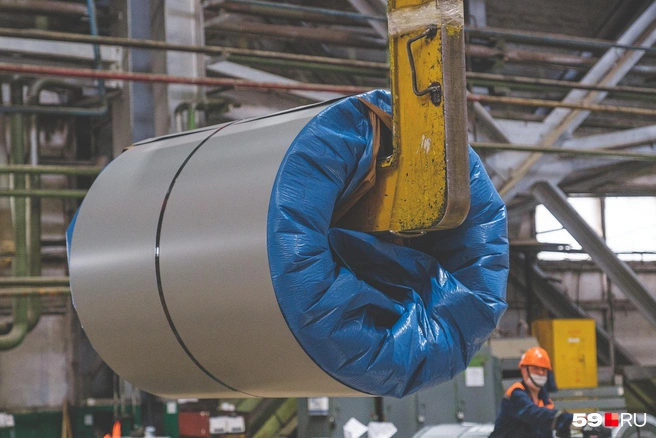
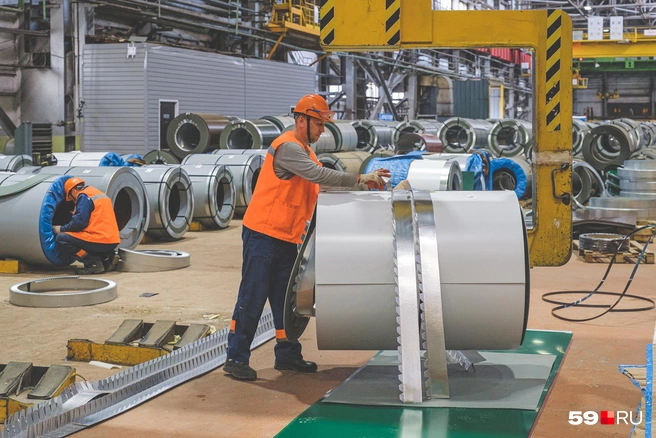
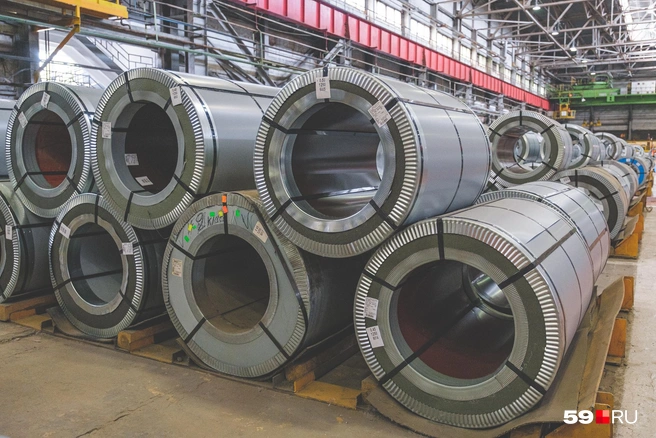
От основания до современности
Лысьвенский металлургический завод основала Варвара Шаховская (урожденная Строганова) в 1785 году. Собственной руды здесь не было, место для строительства выбрали из-за реки Лысьвы: после возведения плотины вода приводила в движение заводские механизмы.
Поначалу на заводе выпускали чугун и изделия из него, потом стали производить металлопрокат и другую продукцию. В XIX веке предприятие обзавелось гербом с изображением единорога — он перешел от нового владельца завода, графа Шувалова. Считается, что клеймо с единорогом имелось на кровле Собора Парижской Богоматери. Документальных подтверждений этому нет, но в 1900 году продукция завода действительно выезжала в Париж — на Всемирной выставке лысьвенское предприятие завоевало золотую медаль.
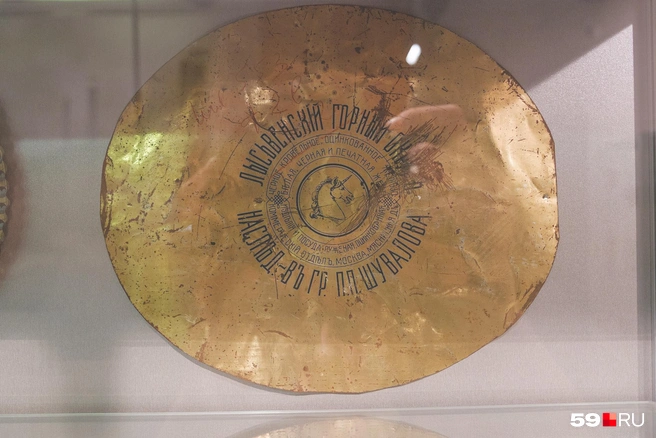
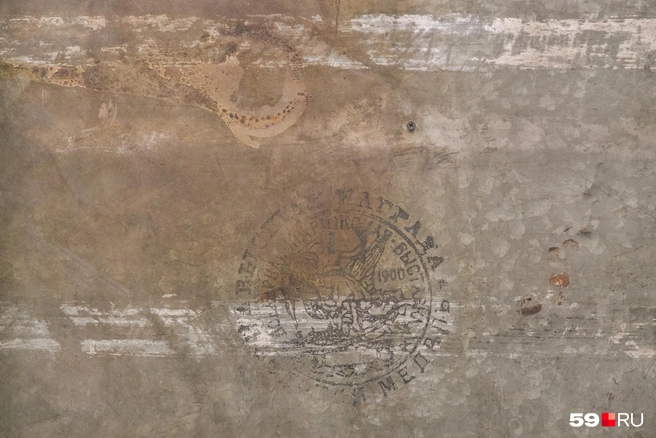
В советские годы ЛМЗ оказался не менее востребованным, чем в царской России. Акцент сделали на выпуск хромированной жести, из которой, в частности, изготавливали консервные банки (в 1929 году — 43% от всей хромированной жести Советского Союза). В 1934 году запустили производство автомобильного листа. Незадолго до этого восстановили цех эмалированной посуды, который открывался в 1913 году.
В годы Великой Отечественной войны завод стал выпускать солдатские каски. Всего на фронт из Лысьвы отправили 10,5 миллиона касок, а также 18 миллионов противогазов и 14 миллионов армейских котелков. К производству тогда привлекали даже младших школьников и детсадовцев: приводили их на пару часов. Но, как рассказывают в местном музее, это делали не из-за нехватки рабочих рук, а для того чтобы подкормить детей: во время смены обязательно делали перерыв на обед в заводской столовой.
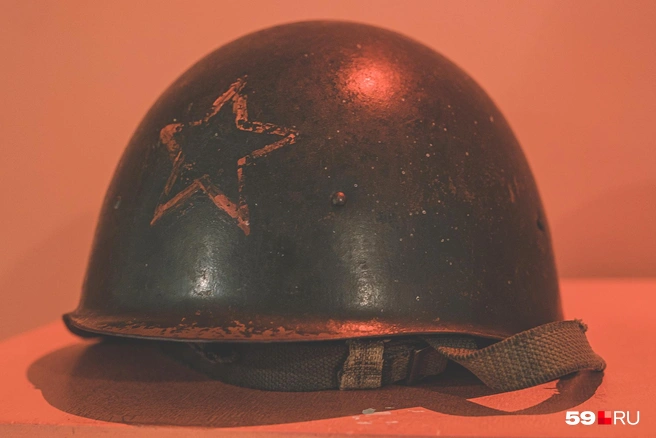
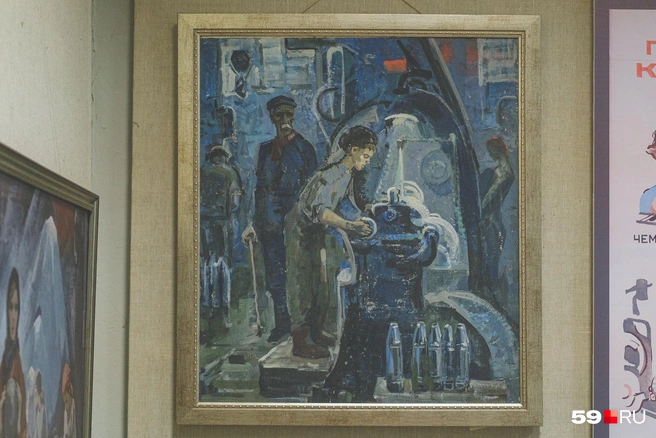
Производство проката с покрытиями зародилось в 1979 году. Тогда на ЛМЗ построили комплекс по производству холоднокатаного листового проката и хромированной жести. Оборудование не раз модернизировали. В 1994 году один из агрегатов перевели на электролитическое цинкование — такой прокат нужен был автомобильной промышленности, после распада СССР потерявшей поставщиков из бывших союзных республик.
С 2017 года Лысьвенский металлургический завод входит в состав группы ММК (Магнитогорский металлургический комбинат).
В прошлом году, несмотря на пандемию, Лысьвенский металлургический завод практически не останавливался. Часть сотрудников вывели на удаленку, но все работающие в цехах продолжали трудиться на своих местах. В итоге выдали 268 тысяч тонн проката с полимерным покрытием.
Ранее мы рассказывали о Лысьвенском заводе эмалированной посуды, поначалу входившем в состав ЛМЗ. А также о заводе бытовой техники в том же городе, где выпускают кухонные плиты.