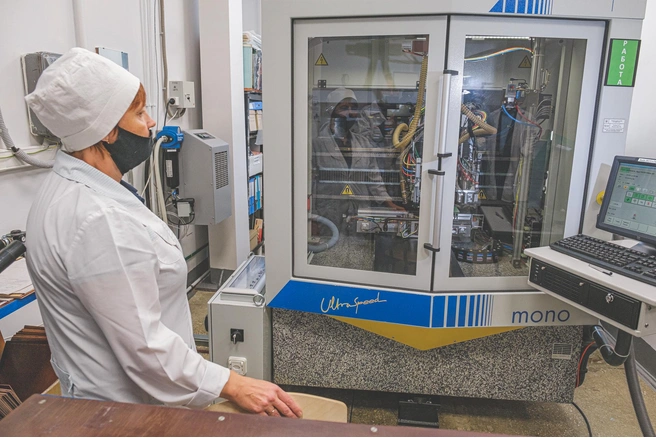
Пермский край всегда славился своей промышленностью. На нашей плодородной земле есть всё — от минеральных солей и угля до нефти и газа, а заводчане составляют значительную часть населения региона. Но есть у Прикамья еще одна заслуга: наш край — один из лидеров в повышении производительности труда на предприятиях. Это помогает укрепить экономическую стабильность региона и продолжать модернизацию производственных мощностей, обеспечивает профессиональный рост работников. Ежегодно на их переобучение направляются десятки миллионов рублей. Растет уровень компетенций, а значит, и заработные платы, улучшаются условия труда.
Благотворно на это влияют и национальные проекты, инициированные президентом России Владимиром Путиным, которые нацелены на повышение качества жизни граждан страны в целом. На территории Пермского края реализуется одна из таких программ — приоритетный нацпроект «Производительность труда». Участие в нем оказывает местным компаниям серьезную поддержку: не только внедряются и развиваются принципы бережливого производства, но и проводится цифровизация и автоматизация труда. На данный момент в нацпроект вступило 97 предприятий Прикамья.
За 2019–2020 гг. в рамках проекта прошли обучение свыше 7000 работников пермских предприятий-участников и 60 учебных заведений Пермского края и России, обучивших специалистов почти по 100 направлениям повышения квалификации и переподготовки кадров.
Цель до конца 2021 года: привлечь к участию 103 предприятия края
Оператором нацпроекта в нашем крае является Региональный центр компетенций (РЦК), который с 2018 года завершил 41 проект на предприятиях. Среди завершивших проект 36 предприятий продолжают развивать производственную систему, а у остальных это запланировано на ближайшую перспективу.
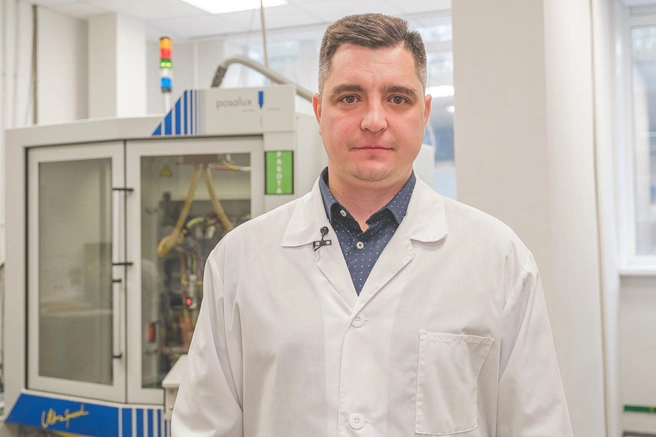
— Производства, которые мы берем на аудит и далее под кураторство в процессе реализации программы, абсолютно разные, — рассказал Алексей Сухорученко, руководитель проектов РЦК в Пермском крае. — Это и пищевая промышленность, и строительство жилых домов и дорог, и металлообрабатывающие производства. Если предприятие работает в приоритетной отрасли, его годовой объем выручки составляет не менее 400 млн рублей и у руководства есть желание идентифицировать проблемные процессы, наладить их, модернизировать и выделить на это необходимые ресурсы, мы всегда готовы оказать ему квалифицированную помощь.
В апреле 2021 года федеральные эксперты признали успешным опыт Прикамья в реализации нацпроекта «Производительность труда», а в сентябре РЦК прошел сертификацию и доказал эффективность своей работы цифрами. Одним из таких успешных опытов по оптимизации процессов предприятия они считают работу с АО «ОДК-СТАР».
Опыт «ОДК-СТАР»: первые итоги и планы
22 сентября вместе с руководящим составом завода представители РЦК подвели итоги работы в рамках нацпроекта. В результате его реализации только за счет организационных мероприятий время производства агрегатов сократилось на 24% — вместо 37 дней сейчас он проходит за 28 дней. Выработка при этом увеличилась на 15%. Сокращение ВВП составило 10%, сокращение НЗП — 6%.
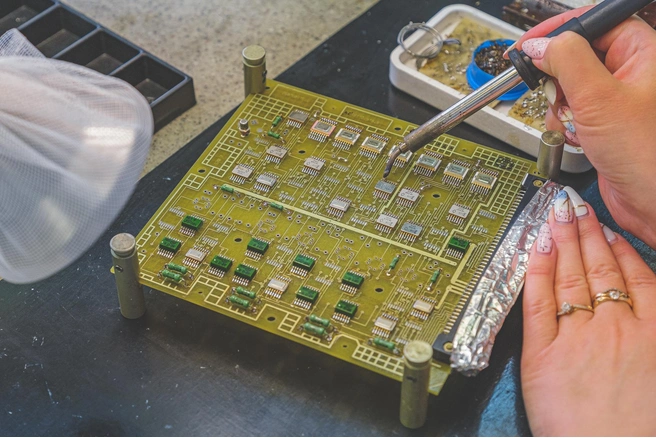
АО «ОДК-СТАР» — предприятие, обладающее компетенциями в разработке и серийном производстве систем топливопитания и управления газотурбинными двигателями воздушного, наземного и морского назначения, включая электронные агрегаты с полной ответственностью типа FADEC и гидромеханические агрегаты, а также имеющее опыт поддержания всего жизненного цикла газотурбинных двигателей. Предприятие входит в АО «Объединенная двигателестроительная корпорация» Государственной корпорации «Ростех».
Пилотным участком, выбранным для повышения производительности в рамках нацпроекта, стало электронное производство «ОДК-СТАР».
— В связи с ростом объема производства по электронным агрегатам нами было принято решение об участии в нацпроекте, — рассказывает Антон Кузнецов, директор по развитию производственной системы АО «ОДК-СТАР». — Были выбраны РД-подобные агрегаты, мы составили карту потока создания ценностей и анализировали потоки, которые проходят на производстве. Смогли выявить проблемные узкие места и сгенерировать план дальнейших действий.
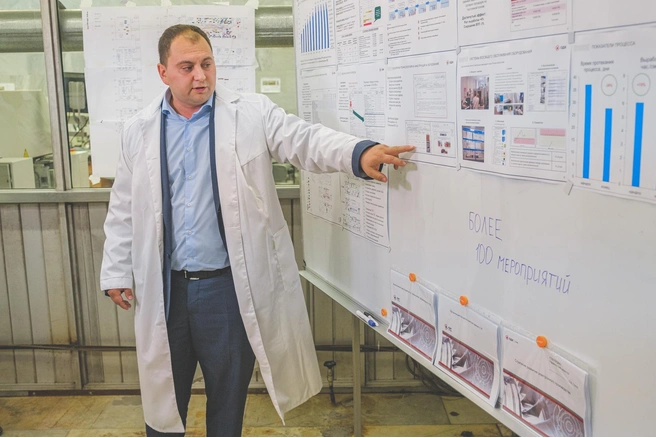
Основными проблемами были: наличие дефицита, длительный процесс контроля, низкий уровень организации планирования, ожидание перехода полуфабрикатов от стадии к стадии, ожидание исполнителя ввиду сменности, длительный процесс переналадки на селективной пайке. По всем направлениям были разработаны организационные мероприятия и мероприятия, требующие капитальных вложений, которые вылились в стратегию развития электронного производства.
— В начале года мы получили задачу по увеличению плана производства в два раза по отношению к предыдущему, — говорит Андрей Кузнецов, начальник электронного производства АО «ОДК-СТАР». — Понимая, что задача перед нами ставится непростая, совместно с РЦК мы разработали программу по увеличению выработки, по улучшению труда рабочих. После ее внедрения в производство монтажный участок был организован в конвейерный вид, время производства конечного продукта на котором сократилось в 2 раза.
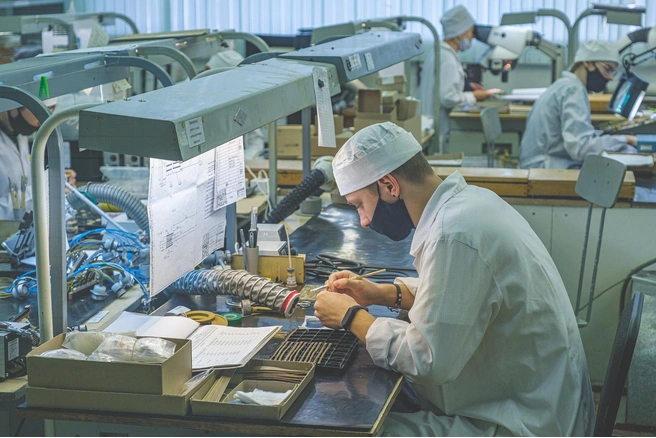
По словам Андрея Кузнецова, на это повлияло даже размещение сотрудников в цехе монтажа. Сейчас все не только взаимозаменяемы в плане функционала, но они даже сидят таким образом, чтобы передавать электронные платы согласно очередности этапов их пайки.
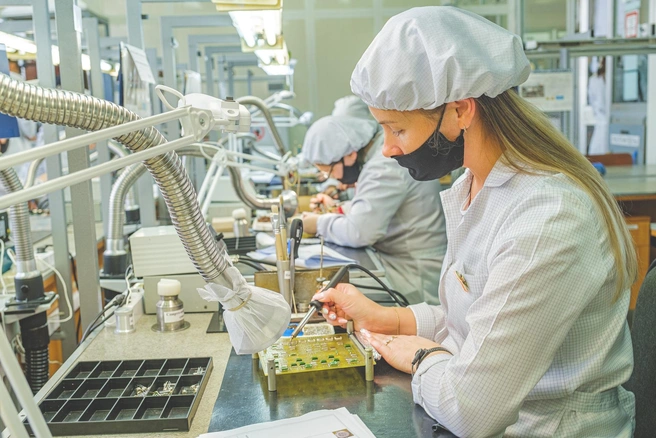
Что касается технических деталей работы, которых коснулась модернизация производства, то и тут можно заметить удобные инструменты работы, которые появились с реализацией нацпроекта на предприятии. Например, раньше, чтобы станок исправно работал, инженер-технолог должен был провести оценку рабочего состояния агрегата, передать при наличии проблему техническому специалисту, после чего задача по ремонту оборудования зависала в воздухе на неопределенное время. Сейчас для этого существует стенд по автономному обслуживанию оборудования на станке Posalux Monokombi, где подробно оценивается состояние станка и время проведения ремонтных работ, если таковые необходимы. Без лишних взаимодействий сотрудников. Все процессы происходят автономно и подразумевают собой гораздо меньшее количество потраченных ресурсов.
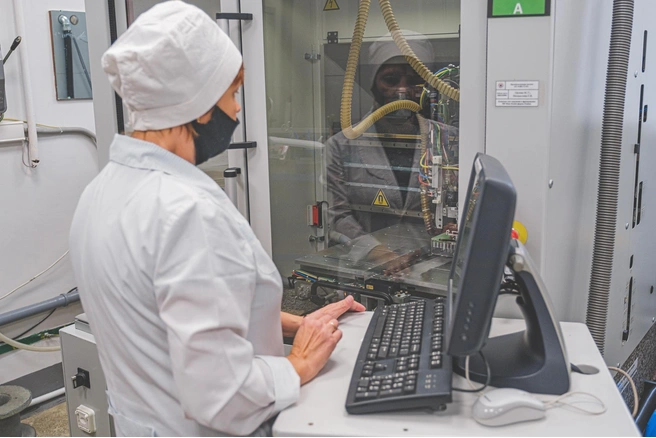
Преемники принципов нацпроекта: швейное мастерство края
Если на предприятии «ОДК-СТАР» уже озвучивают промежуточные итоги работы в рамках нацпроекта, то в ООО «Инициатива» — наследнице Кизеловской швейной фабрики — еще только готовятся к колоссальным изменениям. Сейчас они находятся на стадии первичного аудита предприятия под предводительством Регионального центра компетенций.
ООО «Инициатива» — старейшее предприятие легкой промышленности в Пермском крае. В 2018 году отметило 60-летний юбилей. Большой опыт работы, штат высококвалифицированных специалистов и парк современного оборудования позволяют фабрике изготавливать широкий ассортимент продукции: форменную одежду для силовых ведомств Российской Федерации, специальную и защитную одежду для работы в различных климатических и производственных условиях, медицинскую, гражданскую, детскую и школьную одежду.
— Руководство компании особое внимание уделяет вопросам оптимизации и эффективности производственных процессов, ежегодно инвестирует в модернизацию производства до 10 млн рублей, — рассказала Светлана Кошель, исполнительный директор ООО «Инициатива». — На ближайшую перспективу нами также определены задачи внедрения инструментов бережливого производства, сокращения издержек и потерь, повышения производительности труда и результативности производства в целом.
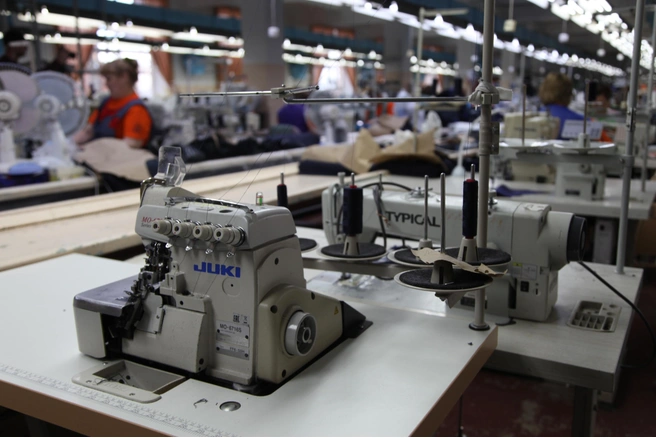
Совместно с экспертами Регионального центра компетенций в рамках нацпроекта «Производительность труда» до конца текущего года на производстве «Инициативы» будет проведена комплексная диагностика деятельности фабрики по всему циклу основного производственного процесса. Рабочая группа, в состав которой войдут ключевые исполнители бизнес-процессов и эксперты РЦК, займется сплошной диагностикой всех процессов на участке пилотного потока — от организации работы склада до отгрузки готовых изделий.
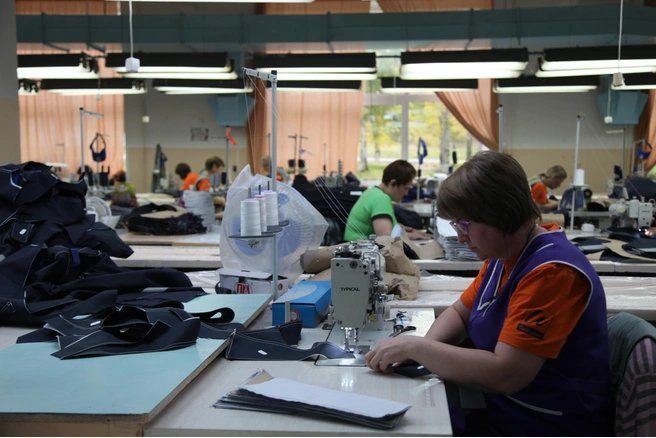
В ближайшее время команда РЦК проведет обучение для сотрудников фабрики, по итогам которого состоится официальный старт реализации проекта.
— Очень бы хотелось видеть вовлеченность сотрудников в процессы реструктуризации производства, в процессы оптимизации швейных и раскройных цехов. От этого зависит эффективность работы всей фабрики.
Национальный проект «Производительность труда» утвержден майским указом президента РФ Владимира Путина в 2018 году и призван создать условия для ежегодного прироста производительности труда в стране на 5% к 2024 году.